A B.C. researcher looking to make the perfect T-shirt has turned to a material so ubiquitous it’s been both a major source of the province’s wealth and the bane of its international trade agreements: softwood lumber.
Stephanie Phillips, a researcher at Kwantlen Polytechnic University’s Wilson School of Design, has been working with colleagues at the University of British Columbia to create a high-quality T-shirt that surpasses all others. Why a T-shirt?
“It's really easy to look at. It's really easy for people to understand. It's what I call an archetypical product,” Phillips said.
The research is the latest B.C.-based effort to try to make the fashion industry more sustainable.
Vancouver’s Canopy has worked with more than 900 clothing and publishing brands, and invested millions of dollars to wean global supply chains off ancient forest products and replace them with recycled clothing and straw.
Phillips, who years ago founded a textile design department at Le Chateau, said her research aims to thread the needle of reducing the environmental impact of fast fashion while sourcing new textiles from sustainable sources.
Fashion on a path to growing pollution
Cotton supplies about a quarter of the fibres used in textiles around the world, but takes up an estimated 2.5 per cent of the world’s arable land and uses immense amounts of water.
Then there are synthetic fibres, which in a 2022 global report were found to make up nearly two-thirds of all clothing. At the time, the industrial processing of all those textiles was found to require more than all the oil consumed in Spain in a year.
Where all that clothing ends up depends on what it’s made off. At the end of its life, a cotton T-shirt can decompose in under a year, whereas past studies have found nylon and polyester clothing require decades to centuries to break down.
“Every second, the equivalent of one garbage truck of textiles is landfilled or burned. If nothing changes, by 2050 the fashion industry will use up a quarter of the world’s carbon budget,” warns the United Nations Environment Programme.
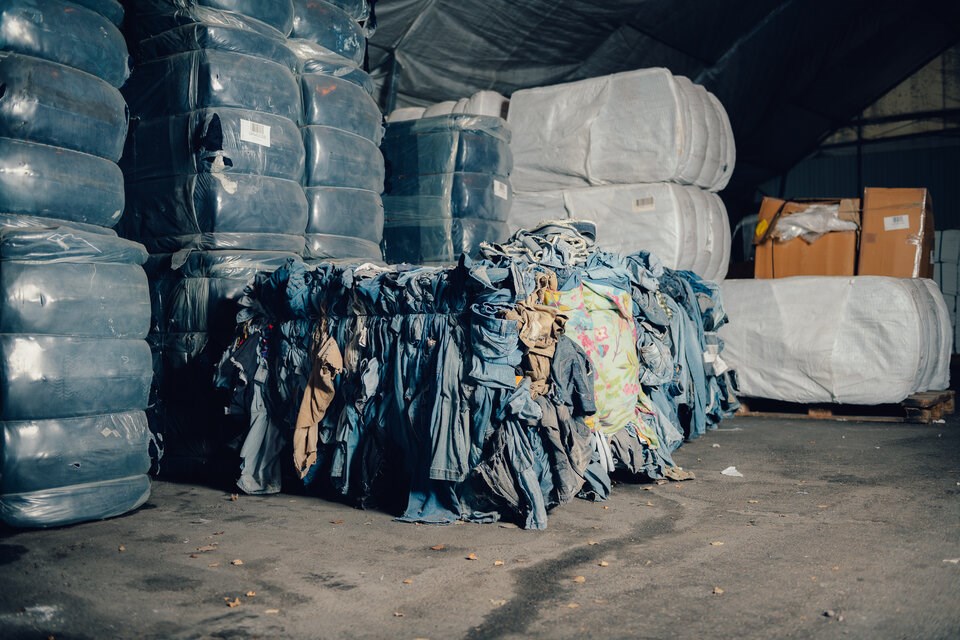
Those who have introduced alternative cellulose-fabrics to the fashion world have tended to use eucalyptus or beech trees. But Phillips says the hardwoods take longer to grow and require more water. Shipping all that material around the world also adds to its carbon footprint.
Using fibres from local softwood lumber is meant to help solve those problems.
The Ministry of Forests has taken a keen interest in the work as it seeks to increase the volume of value-added products to its softwood lumber exports. But Phillips says the research is in its early stages and they have yet to carry out a lifecycle analysis to assess what the environmental impact of such a textile industry would be.
The wider end goal of their research, said Phillips, is to use a waste source of cellulose — including old cotton T-shirts and recycled paper — to create new clothes.
First, they need to know whether they can actually make a good, if not perfect, T-shirt. To rise even close to perfection requires attention to detail.
Reverse engineering the perfect T-shirt
In a bid to understand what defines quality, the team of researchers examined 11 cotton T-shirts ranging from a cheap $4 piece of fast fashion to $400 designer shirts.
The team washed, dried, measured and pulled the T-shirts apart, using textile industry testing standards to gauge abrasion resistance, moisture management transfer, yarn strength and shrinkage. The results were somewhat surprising.
“I bought one $400 T-shirt,” said Phillips. “It's a beautiful T-shirt … but what we've learned so far is that people's perceptions versus value are not aligned.”
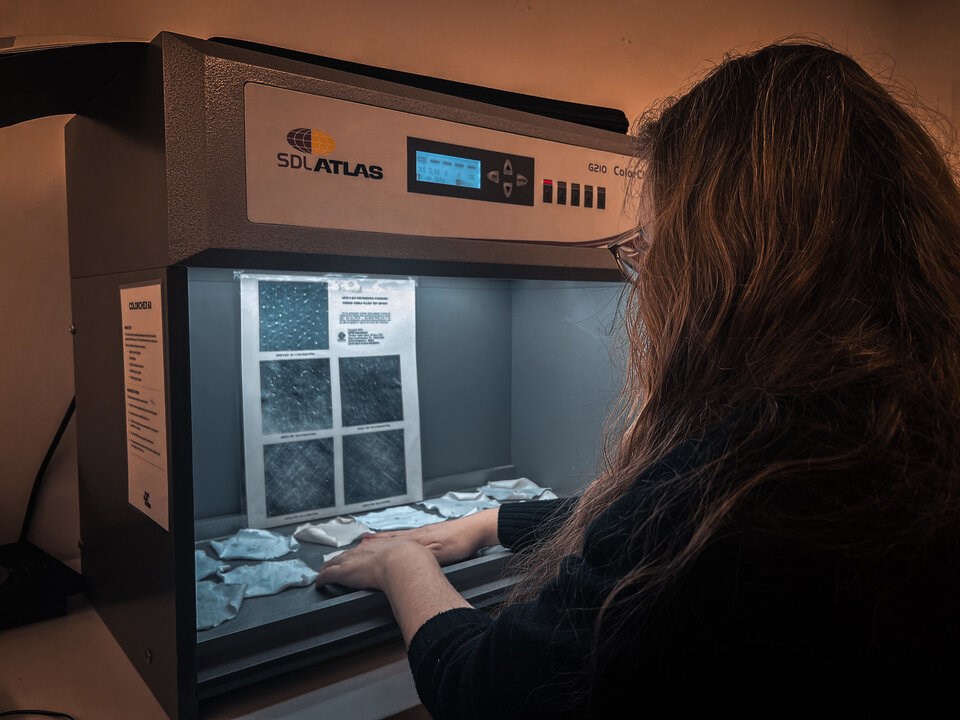
Regardless of price, she found heavier-weight fabrics were perceived as higher quality. Trying to mimic the abrasion resistance of such materials while maintaining the perfect softness is something Phillips says she hopes to replicate in the softwood T-shirt.
The researchers also found the most expensive T-shirts tended to surpass their cheaper alternatives in the quality of stitching.
“If we can get it to be as good as a $400 T-shirt, we will have done something very, very important,” she said. “A lot of the times when we get things from the store, they're quite inexpensive, and they're very cheap.”
“So what I'm hoping to do is increase that quality to allow for a longer wear.”
Scaling up fibre production faces hurdles
Feng Jiang, a researcher at University of British Columbia’s Faculty of Forestry and a Canada Research Chair in sustainable functional biomaterials, has been working with Phillips to create the best textile from scratch.
In the past, Jiang’s research has looked to craft everything from alternative food packaging to cellulose-based conductors and insulating, flame-resistant foams. To create a fibre for clothing, Jiang said his group has had the most success dissolving pulp in a solution and then spinning out a filament.
So far, Phillips said she has received about 60 grams of the fibres, far from the quantity required to create a prototype T-shirt.
“You need kilograms to do trial and error,” said Jiang. “We’ve been trying to see how we can scale this up.”
He said he’s been in talks with a university in China to spin up more prototype cellulose fibres, and that he hopes to get the KPU researcher the material she needs for the T-shirt sometime this year.
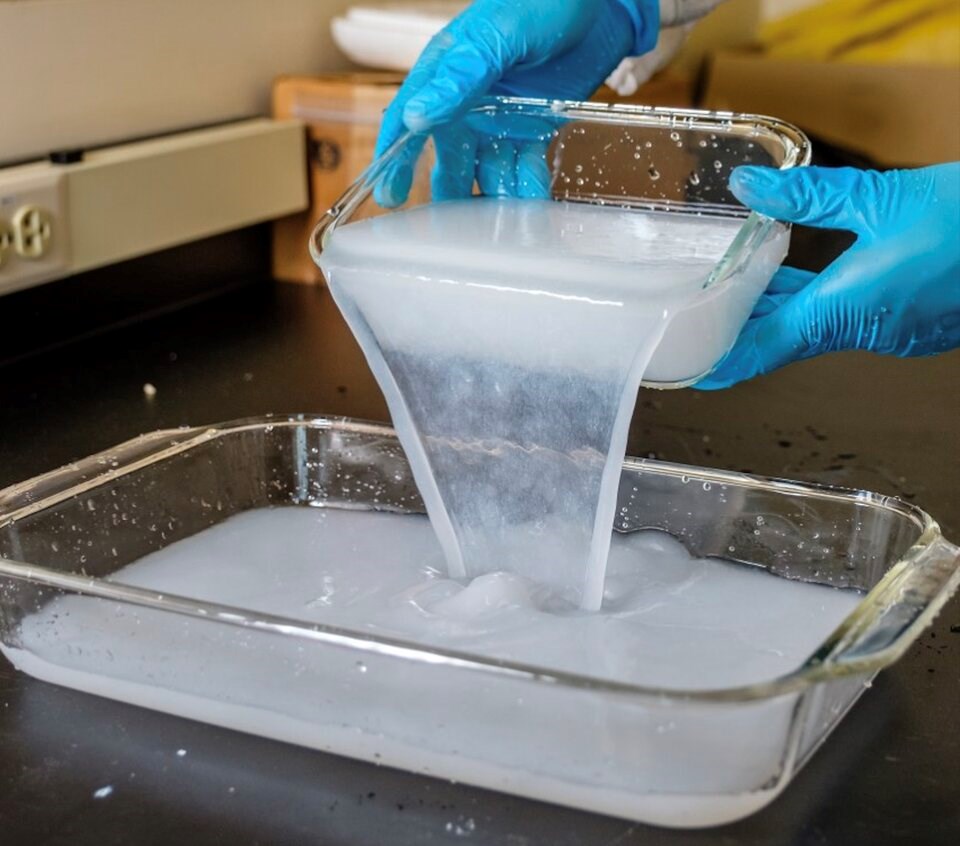
Phillips said the whole experience of creating a perfect T-shirt has been both daunting and exciting. She hopes commercialization, perhaps with a local designer like Lululemon Athletica Inc. (Nasdaq: LULU), Tentree International Inc. or Arc’teryx Equipment, is not too far off.
Once the technology is more refined as a luxury item, the hope is that it will then trickle down into other materials at lower price points.
“Canada hasn't really been a big contributor to the textile industry, and it would be lovely to make our mark, and start having some things that can be made here,” she said.
“We’re going to spin it. And we’re going to knit it. And we’re going to see what happens.”